ASTM A325 structural bolts are most commonly manufactured in one of two ways, cold forging or hot forging. Both methods result in a product that is similar in appearance but are made through a completely different process. Most common size structural bolts, which are readily available in the marketplace, are mass-produced in large quantities using a cold forging method. Custom size structural bolts made in smaller batches are more commonly made using a hot forging process. The reason for this is the hot forging process is less automated and more time-consuming, however, it is necessary if an A325 structural bolt is required that differs in size or configuration than what is readily available. Both methods are summarized below.
Cold Forging – Mass Production
Cutting – When structural bolts are mass-produced, they start out as a long coil of wire, which is fed through a machine to be straightened. This is an important process since any deformation or slight bend can result in a weakness of the bolt. Once straightened, the wire is fed into a shear which cuts it into sections slightly longer than the required bolt length, with the excess length used to make up the bolt head.
- Heading – After the pieces have been cut to length, they are fed into a series of dies that form the head of the bolt. This process is referred to as cold forging since the steel is not heated prior to forming the head of the bolt. The head of the bolt is formed through multiple die hits at room temperature, with each hit shaping the steel, eventually resulting in a hexagon shape. This process is efficient enough to produce tens of thousands of a given bolt size per day.
- Threading – After heading is complete, the other end of the bolt is threaded. This is done using a full-body roll threading process where the end of the bolt to be threaded is extruded down to the pitch diameter and is then fed through two flat threading dies (grooved plates), which rolls or forms the threads onto the bolt.
- Heat Treating – Once threaded, the bolts are heat-treated, which arranges the mechanical properties of the steel to the required strength specified by ASTM. They are put into large ovens in a controlled environment and introduced to regulated temperatures for an amount of time deemed necessary to get the bolt strength into the parameters required by the ASTM A325 specification. This two-part process is referred to as quenching and tempering.
Hot Forging – Custom Size Production
- Cutting – If a structural bolt is manufactured using a hot forging process, the first step is to cut the steel to the appropriate length. Most commonly, the round bar is hot rolled into straight lengths measured at 20 feet, which will then be either sheared or saw cut to lengths slightly longer than the required bolt length. As is the case with cold-forged fasteners, the additional length is the material needed to make up the head of the bolt.
Peddinghaus Shear
Hyd-Mech Bandsaw
- Heading – Once the steel has been cut to the appropriate length, it is time to forge the head on to one end of the bolt. In a hot forging process, one end of the steel rod is heated up in an induction unit before feeding into a National Upsetter used to forge the head onto the bolt. The purpose of this is to make the steel more malleable so that it can be formed easily. A plunger compresses the heated steel to form the heavy hex head pattern of the bolt as well as the required grade stamp and manufacturer’s marking, which is displayed on the top side surface of the bolt head.
- Threading – Once the heading process is complete, the other end of the bolt is threaded. To produce the threaded portion, the hot-forged bolt is cut threaded, a process where the steel is cut away from the round bar of steel to form the threads as opposed to roll threading where the threads are formed through an extrusion process.
- Heat Treating – Once threaded, the bolts need to be heat treated. This is the same two-part process (quench and temper) required for cold-forged structural bolts. They are put into large ovens in a controlled environment and introduced to regulated temperatures for an amount of time deemed necessary to get the bolt strength into the parameters required by the ASTM A325 specification.
5. Galvanizing
Whether cold forged or hot forged, the need for hot-dip galvanizing A325 structural bolts may be required. If so, the galvanizing process is the same for both. The galvanizing process shall be conducted to meet the requirements of ASTM F2329. In this process, bolts are coated with zinc to prevent corrosion.
6. Certification & Testing
Testing – The ASTM A325 specification requires that mechanical testing be performed to ensure that the given batch of bolts manufactured from a certain heat lot of steel meets the strength requirements as stated by the ASTM. In addition, rotational capacity testing may be required, which Per ASTM A325 section 6.3.1 is defined as a test, “that is intended to evaluate the presence of a lubricant, the efficiency of the lubricant, and the compatibility of assemblies as represented by the components selected for testing.” Because this test evaluates the presence of a lubricant, it has only been required when the A325 fastener in question is galvanized. With A325 bolts now falling under the F3125 specification, the rotational capacity test formerly required of all galvanized A325s is now a supplementary requirement (S4), which states, “When specified on the inquiry and order, rotational capacity testing in accordance with Annex A2 shall be performed by the responsible party.”
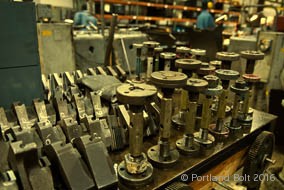
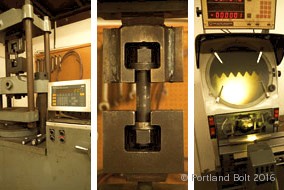
Certification – Certification documents required for ASTM A325 structural bolts consist of the material test reports from the steel mill as well as the results of the mechanical testing performed on the finished fastener. Mill test reports should always be provided with any high strength grade of fastener, regardless of whether the end-user has requested them.